What Are the Effects of L / D on a Single Screw Extruder
This post was last updated on February 1st, 2024
Plastic extrusion is a manufacturing process that creates products by forcing material through a die or an orifice. While this process takes place the end product sometimes comes out semi-finished and requires further shaping.
In this article, we will talk about different dimension extruders and what are the effects of L / D on a single screw extruder.
Contents
ToggleSingle Screw Extruders
Before talking about the effects of L / D on a single screw extruder, let’s understand what single screw extruders in the first place are.
A single screw machine is used mainly to form plastic products by shaping the raw materials into creating the desired object. Plastic is heated until it reaches its melting point. After that, the object is forced into a die, where it assumes its final form.
One of the most popular extruders is the single screw extruder. This machinery gets the job done in very little time. Single screw machines are relatively economic, easy to use, and provide a continuous output.
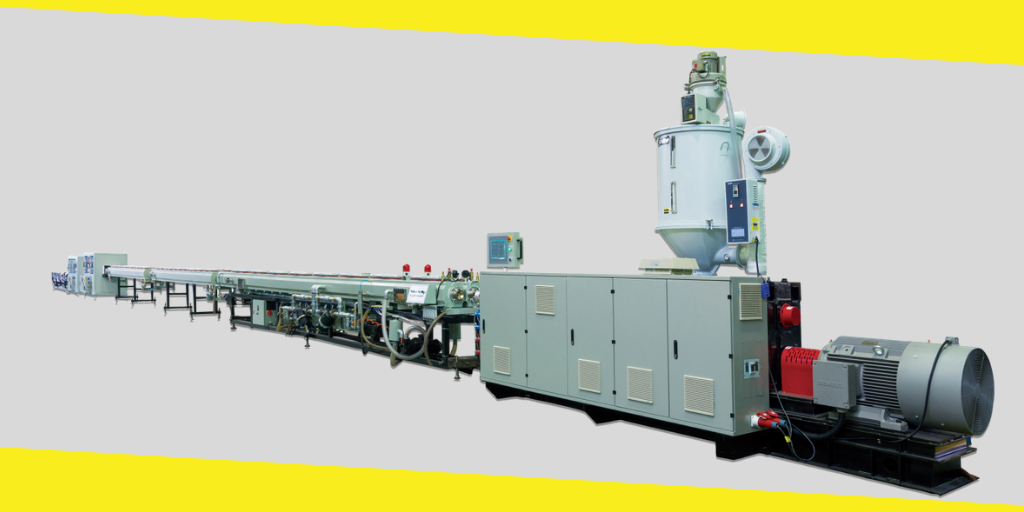
Effect of L / D on Single Screw Extruder
Back in the days, people were operating single screw extruders to produce smaller items. As the demand for larger products grew, limits had to be increased accordingly. It is important to consider the effects of L / D on a single screw extruder as increasing the limits on the output by default has an increase in L/D as well. Keep in mind, that usually these limits are caused by the inability of the feed section to provide more polymer.
When it comes to smaller-diameter screws, the limits generally decide the screw strength. Small screws allow us to go deep in the screw channels. Here the screw does not over-torque and fails. But in larger extruders, the overall efficiency of feeding goes down as the channel gets deeper until there is no more increase in output.
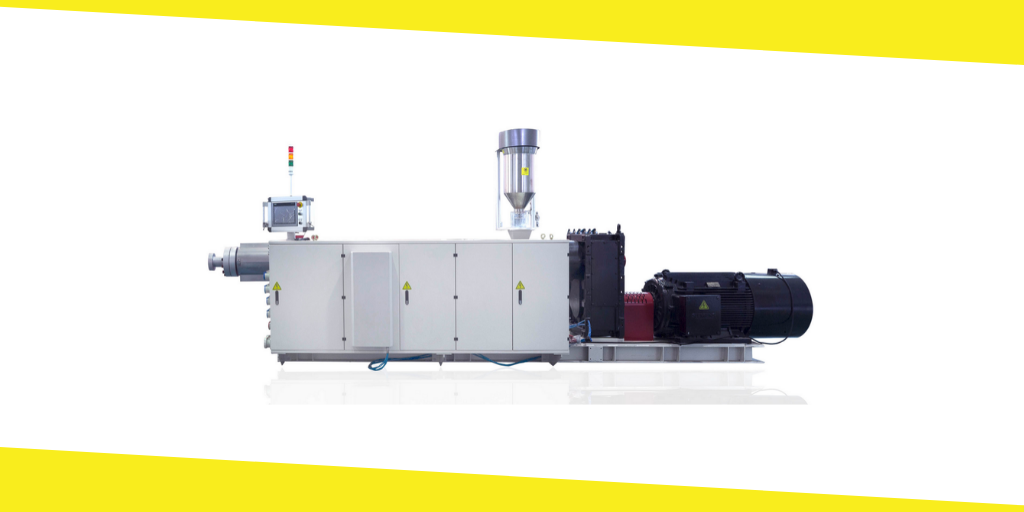
The New Dekuma 38 L / D Extruder
The latest Dekuma 38 L / D is indeed leading-edge equipment. It has an Advanced PCC control system that can be controlled manually as well as automatically. The maximum barrier screw can be used on a wide range of raw materials and articles. It also has the ability to control the specific temperature in the system, ensuring a stable output under varying speeds.
The Dekkuma 38 L / D extruder is similar to the 40 L / D extruder. It has a specially designed groove feeding barrel that fits the screw structure and ensures a steady and consistent production. The robust construct and durability are the reason for its stable extrusion volume and superior product quality. This high performing screw extruder can be controlled independently or through a tandem drive controlled with the main extruder.
Speaking about the effects of L / D on a single screw extruder, the 38L/D extruder energy-efficient performance has an overall higher output (about 25% more) and capacity than the 36 L/D extruder. The 38 L/D extruder is one of the most energy-efficient extruders that Dekuma has made so far and as compared to its lower counterpart the 36 L/D extruder, it can save you up to 20% more energy, while giving you a plastic effect.
Conclusion
Though there are plenty of single screw extruders in the market, Dekuma 38 L/D extruder has outdone itself when it comes to delivering output without compromising the integrity of the product. Being more energy-efficient than its counterparts, the 38 L/D is indeed an innovative piece of machinery and is constructed to re-define extrusion.
If you would like to know more about the effects of L / D on a single screw extruder Dekuma is a well-known international reality, that can help you by providing you with the solution that better suits your needs.
Recommended For You
Septic Safe Toilet Paper: Everything You Need to Know
Arifur Rahman
He is a professional SEO specialist & a freelance writer with a lot of passion to write about technology, startups, travel, lifestyle & other niches. He has contributed to many famous websites. He lives, breathes digital marketing, and helped many companies to grow their business. His main goal is to spread his knowledge that he grabbed in many years and ideas to all generations.