What Is a Spindle Rebuild for a CNC Machine?
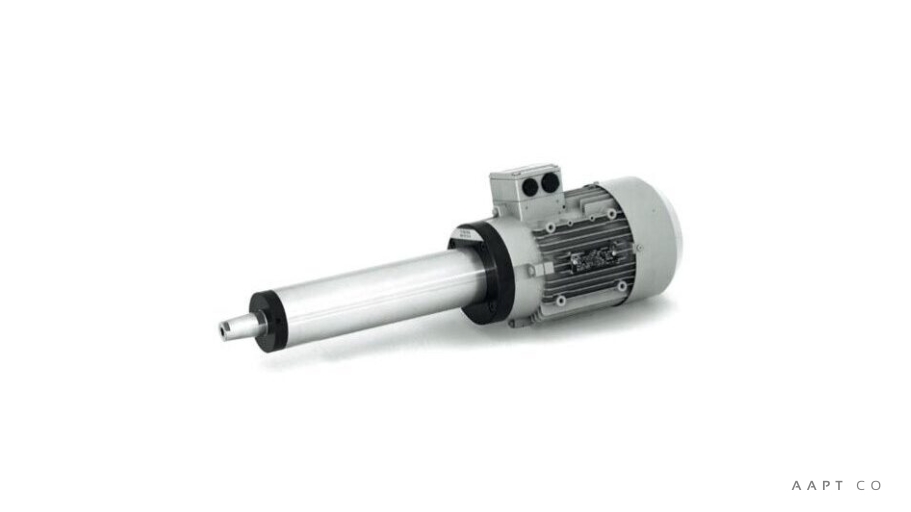
The spindle bearing is one of the most important components of a CNC machine, and if the spindle isn’t functioning properly, you will end up with work that has been cut incorrectly, or the machine won’t function at all. While spindles must sometimes be replaced if they’ve undergone major damage, there are times when they can be repaired or rebuilt. A qualified technician can inspect a failed spindle and determine the best and least expensive remedy. The professional technician often recommends a spindle rebuild, but what exactly is a spindle rebuild for a CNC machine?
Contents
ToggleWhat is It, and How Long Does It Take?
The CNC machine spindle rebuild process is an extensive approach to renewing your spindle so it will function like new. Having your spindle bearing rebuilt instead of replacing it can save you money. A rebuild typically takes 10–14 days, although some service providers can expedite the process.
What Does the Spindle Rebuild Process Entail?
The rebuild process takes as long as two weeks because it’s a tedious, step-by-step process meant to return your spindle to its original condition. Here are the many steps involved in this process:
Step 1 – Inspect & Analyze the Spindle – Before technicians can begin rebuilding the spindle, it is important that they thoroughly inspect and examine the component in the condition it was received. In most cases, the spindle must be properly cleaned before it is inspected and analyzed to determine the problem and develop a plan for rebuilding it. Technicians will perform some or all of the following tests on the spindle to determine why it malfunctioned:
- Pull force
- Run out
- Air purge flow
- Vibration
- And other tests, as determined necessary
Once the evaluation has been completed, technicians will create a Failure Analysis Report (FAR). This detailed report provides information regarding the malfunction, photos, and computer-generated graphs showing the exact malfunction. The rebuild or repair plan is also detailed, and an estimate is provided.
Step 2 – Obtain all Necessary Parts & Begin Repairs – Technicians will perform an extensive search to determine and obtain the best OEM parts necessary to begin the rebuild and repair. Any components that are found to be in functional condition will be cleaned instead of repaired. This step entails the technician searching for any way to improve the overall quality. Technicians can analyze and repair electronics, balance spindles, analyze vibration, repair bearings, and machining to tolerances of 1 micron.
Step 3 – Assemble the Spindle Components in a Sterile Environment – The Technician will assemble the spindle components in a Class 10,000 Hepa Clean room. This ensures that no damaging dirt or debris is introduced to the spindle parts during this part of the process. Even the most minute amount of contaminants could render the spindle unable to function properly, which is why such careful precautions are taken.
Step 4 – Test the Spindle – Testing begins once the spindle has been properly assembled in the sterile environment. Testing helps technicians determine if all the malfunctions have been fixed and whether it performs 100%. The spindle will undergo a variety of tests, all of them simulating the scenarios in which they will be used in your machine shop. During this time, technicians will put the finishing touches on the rebuild or repair. They will also perform any balancing that may need to be done and anything else that technicians determine needs to be done.
Step 5 – A Final Report is Prepared – A final report will be drafted once all repairs and tests have been completed. This report will include details of the specific repair and rebuild tactics used. It will also show how your spindle may perform as it was when it was brand new. In some cases, the technician will have enhanced its level of functionality beyond what it was originally. If this is true, then it will be indicated in the report. The rebuild or repair will come with a warranty in most cases.
Can a Spindle Undergo Multiple Rebuilds?
As long as a technician determines that a spindle can be rebuilt, it can undergo this process as many times as necessary. However, if you and your team practice proper maintenance on the spindle, it will decrease the number of times it fails and, therefore, require fewer repairs or a rebuild. Rebuilding and repairing a spindle is a lengthy and strategic process that only a professionally trained expert can perform. While the workers who run the CNC machines and use the spindles might believe they can repair or rebuild a spindle, it’s best to leave it to the experts, as the workers don’t have access to everything necessary to perform a job equivalent to what the OEM can.
The original equipment manufacturer is the best company to repair or rebuild for several reasons. Firstly, they can easily obtain all the high-quality OEM parts to renew the spindle. Another reason why the OEM is the best company to repair or rebuild a spindle is because they’re specially trained to perform such specific repairs, and the warranty guarantees their work.
As you can see, this is a very detailed and extensive process that will be involved in rebuilding or repairing your spindle bearing. Hopefully, once the spindle is returned to you, it will work better and more efficiently than it ever did in the past. If, for some reason, it doesn’t, then you can contact technicians, and they will inspect the spindle to determine what they may have missed. However, the rebuild will succeed in most cases, and the spindle will work optimally.
Recommended For You
Best Brands of Modular Switches in India
Most Inside
Most Inside offers high-quality recommendations and valuable updates to enhance all aspects of your life, providing premium guidance and enriching experiences.